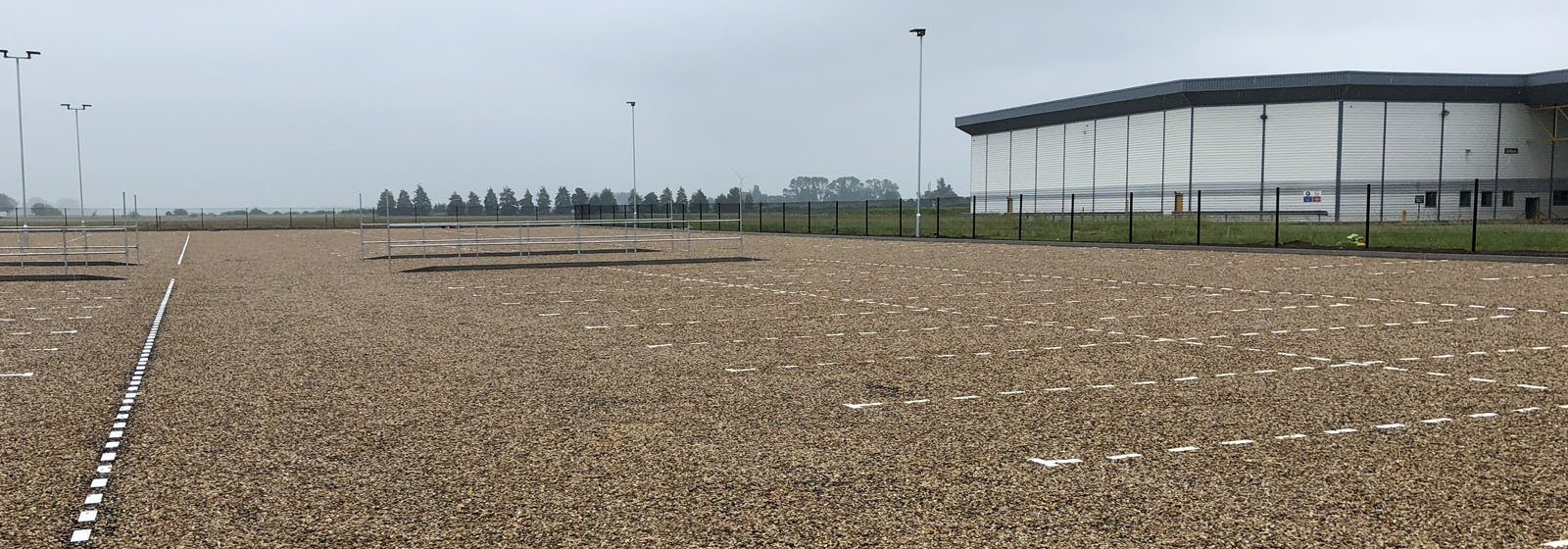
Princes Foods West Car Park
ONE was commissioned by the main contractor, adi Building & Refurbishment, to design a new 400 space car park for...
Find out moreHQ: +44 (0) 1905 362 300 | London: +44 (0) 208 0596 526 | Birmingham : +44 (0) 121 312 3876 | Cardiff : +44 (0) 2920027983 |
HQ: +44 (0) 1905 362 300 | London: +44 (0) 208 0596 526 | Birmingham : +44 (0) 121 312 3876 | Cardiff : +44 (0) 2920027983 |
Having successfully completed the new West Car Park for Princes Group’s largest food production site in the U.K. at Long Sutton, Lincolnshire, ONE’s architects and civil and structural engineers were commissioned by adi Building and Refurbishment to design a new Raw Materials Warehouse with Cold and Chill Store, office and loading bays.
Long Sutton, Lincolnshire
adi Building & Refurbishment
£22m
Civil & Structural Engineering, Architecture,
The requirements for the extension to this crucial facility included provision for: food processing and storage (including cold stores and freezers), raw materials shuttle racking, cooking and preparation spaces and logistics for HGV to forklift truck loading and unloading of materials and finished items.
The extension is 12,389m² (133,354ft²) constructed from an open span steel frame. The design provides flexibility for future use and includes a mezzanine with high loading capability for further usable space.
ONE’s multidisciplinary team provided best value to the client and hundreds of thousands of pounds were saved, for example, through the ground improvement techniques. A Vibro Stone Column ground treatment system was used to support the building foundations and the ground floors of the processing area while a Rigid Inclusion Ground Treatment system will support the raw materials warehouse slab. ONE has used these types of ground improvement measures on many of our projects often saving our clients time and money.
Revisions to the architectural approach also improved the appearance, functionality and cost of the building as well as saving materials and time on site.
There were a range of challenges such as the site is located in rural Lincolnshire and is incredibly flat. Storm water and overland flooding were, therefore, vital environmental issues and the design met the local authority’s SUDS requirements. The storage and pump system were carefully incorporated with a very complex stainless-steel trade effluent system which was also required for food hygiene.
The design had to interface with various existing elements on site with careful consideration to the requirements of the food processing industry, for example, the relationship of the new facility with the existing building which is used for processing peas and minimising disruption to this area at seasonal time-critical harvesting.
ONE’s team is not afraid of challenging a design to make it more efficient and saved the client hundreds of thousands through a range of measures.
ONE’s expertise and insight into the industry meant that the design minimises the client’s risk. All aspects have been considered with regards to hygiene, avoidance of disruption or downtime for food processing/production and the extension interfaces perfectly with other existing buildings.
The multi-disciplinary team worked together to find solutions to ensure the best possible design for the client.